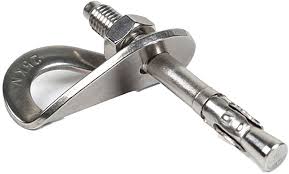
Equipement des voies d’escalade
Assurément je réponds affirmativement NON !
Si nous voulons être tranquilles par rapport à l’usure des matériaux de sécurité posés en falaise (en milieu marin ou pas), une seule réponse est 99% fiable … le Titane. Je ne dis pas 100% car le 100% en matière de sécurité est inatteignable. Certes on est certain qu’il ne corrodera pas, mais c’est du matériel scellé et la tenue des résines servant à la pose implique un autre questionnement ! Pour rassurer les résines n’étant pas destiné uniquement aux grimpeurs mais à l’industrie les normes sont fiables et faciles à analyser … reste à maitriser la pose et la qualité du mélange en sortie de buse (pose d’un test à chaque cartouche).
Donc OUI le titane je vote pour … seul problème le prix ! Environ 10€ la broche et 70€ le relais sans la résine … ceux qui pensent qu’on équipe trop vont être satisfait et les rééquipements risquent d’attendre
Pour rester réalistes et néanmoins sécuritaires, tout le monde vante alors l’inox … qui c’est exact est un acier inoxydable ! Tout le monder répète cela et nos fonctionnaires FFME nous ont pondu des textes affirmant que seul l’inox devait être utilisé.
Sur le web j’ai poussé un petit voire gros coup de gueule à propos de ce délire sur la sécurité des ancrages et l’imposition de l’inox comme seule alternative !
Ce petit pamphlet m’est venu à l’esprit en découvrant que le CT38 payait 200 goujons inox pour rééquiper une voie aux Gillardes ! Alors que le CT38 pleure misère et nous vend un ZE topo à un prix frôlant l’escroquerie …
Alors je dis stop, dans une falaise non marine, poser de l’inox, c’est balancer le fric par les fenêtres !
Avis péremptoire me direz-vous (débattu plus avant) … quand j’affirme que c’est juste jeter l’argent par les fenêtres et donc de la pure bêtise démago sécuritaire, sans aucune justification que de poser de l’inox aux Gillardes
Tout comme le CT01 qui m’a demandé pour Virieu le Grand des relais inox et qui a refusé de croire en mes arguments … bon le club Hot Roc en a offert 10 alors qu’ils en auraient eu 30 … on ne raisonne pas les gens bornés !
Pourquoi J’AFFIRME que mettre de l’inox en milieu non marin n’est pas une obligation … alors que je ne suis pas ingénieur et que comme tous les béotiens je me suis jeter sur l’inox au début … posant du 304 qui s’est avéré ensuite pire que tout ! Réalisant cela, j’ai écouté beaucoup d’avis et surtout ceux de personnes travaillant sur l’inox pour d’autres raisons que poser des points d’assurage
Une certitude, l’inox est très mal maitrisable par un grimpeur/équipeur et pas plus par les penseurs de la FFME et du Comité National escalade, qui n’ont fait que relayer une étude de l’UIAA où participait l’ENSA (faut bien s’occuper) !
Poser de l’inox suppose de l’inox de qualité … au minimum 316L et il faut être certain que rondelles et écrou sont en 316L aussi (sans oublier la petite bague qui sert à expanser le goujon) … et il faut poser le goujon avec un marteau à tête inox (un marteau à tête acier affaiblit l’inox et débute la CSC) … et la plaquette doit être du même inox ! Si tous ces paramètres ne sont pas en adéquation, c’est pire que l’acier, la CSC (corrosion sous contrainte) se déclenchera à tous les coups. Précison je donne les normes chiffrées de l’inox (type 316L … 316Ti … 317) car je ne suis pas arrivé à faire coïncider le terme HCR ou PLX (Fixe) avec ces normes.
Ne pas oublier que en cas de choix de poser de l’Inox, le meilleur c’est de poser de l’inox 316Ti (ce que nous utilisons avec mes amis Suisses à kalymnos) là c’est garantie 25 ans à la CSC (et ça a été étudié pour le tunnel du Gothard où les résurgences sont salines) … il existe encore mieux comme inox (garantie 50 ans à la CSC) mais c’est impossible à acheter pour des quantités propres à de l’équipement … et de toute façon le coût est exorbitant.
Le mieux … même en milieu marin semble être les broches scellées de type Brouet Badré en galva … les tests faits à la triperie dans les calanques au bout de 25 ans sont assez probants ! Si on n’a pas le courage de coller en milieu marin l’inox 316 L est un minimum sécuritaire incontournable … là c’est certain !
Mais en milieu non marin type l’Isère, il est TOTALEMENT DEBILE de dépenser du fric pour poser de l’inox … les aciers classiques tels ceux posés dans les années 80 ont prouvé que 40 ans après tout va bien … surtout le vieillissement de l’acier est facilement visible à l’œil nu … pas la CSC de l’inox !
CE QUI EST PASSE SOUS SILENCE par les pros inox de partout, c’est que son vieillissement est angoissant car on arrive difficilement à maitriser le matériel (goujon + bague + rondelle + boulon + plaquette) en qualité identique !
Si on veut vraiment à tout prix (et jeter l’argent par les fenêtres) poser de l’inox le mieux, et le moins angoissant, c’est comme Piola de sceller des broches inox (de qualité 316L ou 316Ti) … pas de contraintes car pas de serrage, une seule pièce et pas de frappe donc peu de risques de CSC ! Mais dans le cas de broches soudés des problèmes de CSC sont apparus !
En milieu marin agressif on n’a pas le choix, vu qu’on n’a pas les moyens du titane, on pose donc de l’inox ! Mais il faut savoir que c’est parfois une bombe à retardement si tout ce que j’ai énoncé n’est pas maitrisé à 100% !
En milieux non marin ce danger potentiel, est bien plus important que de poser des plaquettes et goujons en acier (le rééquipement de Presles à 30 ans d’âge et rien ne bouge) les broches Brouet Badré de Mouries ou Buoux sont impeccables après bientôt 40 ans .
Donc oui j’AFFIRME que poser de l’inox en dehors de certaines falaises spécifique, est une pure idiotie … Bon je ne suis pas sûr que les fonctionnaires fédéraux à la philosophie bretelles + ceinture entendront mon message … et je n’en ai rien à battre d’ailleurs (en plus je n’équipe pratiquement plus) … juste je voulais que le commun des grimpeurs sache que ce qui est écrit dans les manuels FFME, et affirmé par les bureaucrates des CT n’est pas toujours la vérité !
Un peu comme quand on essaye de nous faire croire que pour s’encorder en dehors du nœud en huit il n’y a pas d’autre alternative ???? Le nœud de guide reste celui que j’utilise (il porte en son nom même un gage de sécurité) et si un initiateur FFME fraichement diplômé essayait de me faire changer mon encordement sur une SAE … il se fera jeter proprement !
En résumé, conclusion personnelle … et j’admets que d’autres ne partagent pas mon jugement !
Le TITANE c’est le must !
Avantages : Dans 100 ans toujours pas de corrosion,
Inconvénients : Très onéreux et pas facile à se procurer, nécessite de sceller
L’INOX : Ça peut être excellent comme son contraire ! Utiliser uniquement de l’inox haute résistance à la corrosion (316L ; 316ti et au dessus)
Avantages : C’est un bon compromis en milieu salin chaud et humide.
Inconvénients : Dans le cas des goujons, ça demande beaucoup de connaissances et de précaution pour mettre en adéquation toutes les pièces du point d’assurage (tige fileté, bague d’expansion, rondelle, boulon, plaquette doivent être d’un inox identique (corrosion par contact) … frappe pour enfoncer le goujon devant être effectué avec une masse ad hoc (corrosion par piqûre).
Dans le cas des tiges inox à sceller beaucoup moins de CSC potentielle, seule la soudure peut poser problème.
Prix un peu élevé qui demande donc son utilisation qu’en cas de besoin impérieux.
Autre inconvénient … la CSC ne se voit pas toujours car elle est interne au métal
LES BROCHES GALVANISÉES (type Brouet badré) : Semble le meilleur rapport qualité prix dans tous les milieux, plus de 40 ans de retour d’expérience le démontre
Avantage : peu onéreuses
Inconvénients : demande de percer à 14mm dans le cas des broches Brouet Badré, et demande de sceller … et le problème des colles et de leur tenue dans le temps est à étudier
LES ACIERS SIMPLES : Semblent être à l’expérience du temps (3 à 4 décennies) suffisant en milieu continental européen
Avantages : peu chers
Inconvénients : Finit un jour ou l’autre par rouiller
Documentation du fabricant WURTH
1. LES ACIERS
La norme ISO 898-1:2013 spécifie les caractéristiques mécaniques et physiques des vis, tiges filetées et autres éléments constituant les chevilles en acier au carbone et en acier allié, testé dans la plage de température ambiante de 10°C à 35°C.
Les aciers standards les plus couramment utilisés pour la fabrication de chevilles sont répertoriés selon leur classe de résistance, comme indiqué dans le tableau ci-après : dans lequel fuk indique la tension de rupture caractéristique et fyk la limite élastique caractéristique de l’acier.
Les aciers sont généralement protégés contre la corrosion par un revêtement additionnel. Les principaux types de traitement sont le zingage ou la galvanisation à chaud.
Le zingage consiste à surcoucher l’acier d’un revêtement de zinc de 5 μm, selon la norme EN ISO 4042.
La galvanisation à chaud, ou plus exactement la « galvanisation à chaud au trempé », est une technique de l’industrie de lamétallurgie qui est utilisée pour renforcer une pièce d’acier à l’aide de zinc, dans un bain de zinc en fusion à 450°C environ.
Ce procédé donne au revêtement protecteur de l’adhérence, de l’imperméabilité, et de la résistance mécanique. Une pièce traitée par la galvanisation est dite galvanisée.
C’est un principe qui conjugue les 2 types de protection, physique par enrobage de la pièce, et chimique par apport d’un métal. Le traitement doit être conforme à la norme ISO 1461 (« Revêtements par galvanisation à chaud sur produits finis en fonte et en acier »). Ce procédé ne consiste pas uniquement à déposer du zinc sur quelques micromètres à la surface de l’acier.
Le revêtement de zinc est chimiquement lié à l’acier de base, car il se produit une réaction chimique métallurgique de diffusion entre le zinc et le fer ou l’acier. Quand on retire l’acier du bain, il s’est formé à sa surface plusieurs couches d’alliages zinc-fer sur lesquelles le zinc entraîné se solidifie.
Ces différentes couches d’alliages plus dures que l’acier de base pour certaines, ont une teneur en zinc de plus en plus élevée au fur et à mesure que l’on se rapproche de la surface du revêtement.
LA GALVANISATION
AVANTAGES
1. La galvanisation permet d’obtenir un enrobage total de la pièce (intérieur et extérieur), sans qu’aucune zone ne soit laissée sans protection, c’est donc de très loin la protection la plus efficace.
2. La galvanisation a l’avantage de la « double protection » :
• Protection physique par enrobage,
• Protection électrochimique (le pouvoir sacrificiel du zinc).
3. L’épaisseur du revêtement est importante : 45 microns.
4. le revêtement après galvanisation est très adhérent : il se crée un alliage métallique.
INCONVÉNIENTS
1. La galvanisation consistant à plonger les pièces dans un bain de zinc en fusion à 450°C, il en résulte des risques de déformation des pièces fines.
2. Résidus de zinc lors de la sortie de la pièce, (coulures, grattons, etc.) et irrégularités de surface dues à l’épaisseur de zinc déposée 45 microns). Ces irrégularités d’aspect inhérentes au traitement ne peuvent pas être considérées comme des défauts.
3. Les trous et filetages sont obstrués par le zinc en fusion, ce qui nécessite un perçage ultérieur.
4. Difficulté à peindre car il y a des risques de dégazage lors du thermolaquage ultérieur avec apparition de bullage de surface.
Le zingage électrolytique occupe une position dominante dans le domaine de la galvanoplastie par le tonnage de métal électro-déposé. Les dépôts de zinc brillants sont très largement répandus et les électrolytes se sont développés pour donner aux dépôts des propriétés recherchées en termes d’aspect décoratif, de résistance à la corrosion et d’aptitude à la passivation au chrome. Le zingage électrolytique est appliqué pour résister d’abord à la corrosion avant toute considération esthétique ou fonctionnelle. La protection contre la corrosion de l’acier est d’abord le fait de la différence de potentiel anodique entre le zinc et le fer contenu dans l’acier. L’acier est ainsi protégé par protection cathodique aussi longtemps que le zinc ne sera pas complètement oxydé. La capacité du dépôt à réduire la vitesse de corrosion se résume simplement à 4 variables :
• L’épaisseur du dépôt communément située à 5 microns aujourd’hui ;
• Sa capacité à recevoir des couches de conversion protectrices d’épaisseurs de l’ordre de 200 à 400 nm dans le cas des conversions au chrome trivalent ;
• La diminution de la différence de potentiel avec l’acier par l’utilisation d’alliages plus nobles tels que le Zn-Ni à 12-15 % en nickel ;
• Le dépôt d’une finition renforcée de type organo-minérale utilisant de la silice, des lubrifiants et des inhibiteurs sur une épaisseur de 1 μm.
Les électrolytes de zingage se répartissent en 2 types : alcalins ou acides.
L’ÉLECTRO ZINGAGE
AVANTAGES
1. Cette technique est plus douce que la galvanisation.
2. L’électro-zinguage permet le traitement sans déformation.
3. La surface obtenue est extrêmement lisse, et après peinture on obtient un aspect parfait.
4. Le revêtement est très adhérent.
INCONVÉNIENTS
1. Épaisseur du revêtement moins importante
2. LES ACIERS INOXYDABLES
Les aciers inoxydables, couramment appelés inox sont des aciers auxquels on ajoute une forte proportion de chrome (> à 10,5 %). Cet élément leur confère une excellente résistance à la corrosion, une inoxydabilité. Le but des aciers inoxydables est d’avoir un matériel en acier très résistant à la rouille et la corrosion et résistant aux :
• Conditions atmosphériques défavorables tel que le dioxyde de carbone, l’humidité, les champs électriques, le soufre, le sel, et les composés de chlorure.
• Substances chimiques produites naturellement ou artificiellement (par exemple : l’ozone).
• Conditions extrêmes telles que des températures très élevées.
L’acier inoxydable est 100 % recyclable. En fait, plus de 50 % d’un nouvel acier inoxydable est fait à partir des chutes de métal refondu, le rendant bon pour l’environnement. La norme DIN EN ISO 3506 s’applique aux vis et écrous en acier inoxydable. Il existe un grand nombre d’aciers inoxydables qui sont répartis en trois sous-groupes :
• Les aciers austénitiques (les plus courants).
• Les aciers ferritiques.
• Les aciers martensitiques.
Système d’identification ISO pour le groupe des aciers austénitiques :
Il y a plus de 150 types d’acier inoxydable, classés en diff érentes catégories selon la composition.
Composition des aciers inoxydables les plus courants
En cas de sollicitations corrosives importantes, il convient d’utiliser des aciers chrome – nickel – molybdène du groupe A4. Seules les chevilles en inox A4 peuvent être posées à l’extérieur conformément à leur ATE. Si l’on s’appuie sur l’Eurocode 3 « Calcul de structures en acier » NF EN 1993-1-4, on peut lire en annexe A 4.1 que la nuance d’inox dite HCR (Haute Résistance à la Corrosion) [1.4529] est adaptée aux applications structurelles en environnement marin à risque élevé et tunnel routier avec salage. Comme par exemple les fixations d’éléments porteurs situés dans des atmosphères chargées en chlorures ne pouvant faire l’objet d’un nettoyage régulier avec une eau contenant plus de 250 mg/l d’ions chlorures. (voir tableau ci-contre) La norme allemande Z30.3-6 va encore plus loin en le préconisant pour les stations thermales (présence d’ion chlorure et de chaleur).
3. PHÉNOMÈNES DE CORROSION DE L’ACIER
La corrosion désigne l’altération d’un objet manufacturé par l’environnement. La corrosion a des causes à la fois physico-chimiques et mécaniques.
Les exemples les plus connus sont les altérations chimiques des métaux dans l’eau (avec ou sans oxygène), tels la rouille du fer et de l’acier ou la formation de vert-de-gris sur le cuivre et ses alliages (bronze, laiton). Dès qu’un métal est en présence d’oxygène, son oxydation commence instantanément. La corrosion des métaux est un phénomène naturel.
La corrosion des métaux est dans la grande majorité des cas une réaction électrochimique (une oxydoréduction) qui fait intervenir la pièce manufacturée et l’environnement.
Le matériau dont est faite la fixation n’est pas le seul facteur conditionnant la vitesse du processus d’oxydation, puisque la forme de la pièce et les traitements subis (mise en forme, soudure, vissage) jouent un rôle primordial. On distingue la corrosion généralisée qui se forme lorsque l’acier inoxydable est en contact avec un milieu acide et la corrosion localisée qui se rencontre dans la majorité des cas lorsque l’inox est placé dans un milieu neutre chloruré. Le processus de corrosion peut également être ralenti en agissant sur la réaction chimique en elle-même.
Il existe 3 types de corrosion :
• La corrosion par contact.
• La corrosion par piqûres.
• La corrosion sous contraintes.
La corrosion par contact naît d’un assemblage de 2 métaux différents (par exemple 2 nuances d’aciers, ou le même acier traité différemment), peut créer une corrosion accélérée ; on voit d’ailleurs souvent des traces de rouille au niveau des écrous. La corrosion est donc un phénomène qui dépend du matériau utilisé, de la conception de la pièce (forme, traitement, assemblage) et de l’environnement.
La corrosion par piqûre est la rupture locale du film de passivation de l’acier inoxydable provoquée par un électrolyte riche en chlorures et/ou sulfures. A l’endroit de la piqûre, le métal est mis à nu, la corrosion va se développer si la piqûre ne se repassive pas, donc si la vitesse de dissolution du métal permet de maintenir un environnement suffisamment agressif pour empêcher sa repassivation. On désigne par « corrosion sous contrainte » la formation de fissures qui démarrent après une période d’incubation plus ou moins longue et qui ensuite peuvent se propager très rapidement et provoquer une rupture brutale par fissuration. Ce phénomène, particulièrement dangereux, se produit par effets combinés de 3 paramètres :
• La température : la corrosion sous contrainte se développant rarement en dessous de 50°C.
• Les contraintes appliquées ou résiduelles subies localement par la pièce.
• La corrosivité du milieu : présence de Cl-, H2S ou milieux caustiques NaOH.
Les aciers austénitiques A4, sont plus résistants à la piqûre de corrosion que les aciers ferritiques au chrome.
En chevillage, la seule solution contre la corrosion sous contrainte reste l’acier HCR.
Bruno Fara
Articles de cet auteur
fr
Equipement des voies
?
|
OPML
?
Site réalisé avec SPIP 3.1.1 + AHUNTSIC
Visiteurs connectés : 10